“Struck by a moving vehicle” is the second most common cause of workplace fatality, accounting for 25 deaths in the year 2020/21.
In addition, every year there are fatalities and serious injuries involving forklift trucks which could have been prevented if properly trained staff had followed safe systems of work.
Nobody should operate a forklift truck, even on a very occasional basis, if they have not received the appropriate training. Employers are required to provide training and testing for all lift-truck operators they employ, and to ensure that anyone operating workplace transport on their sites is competent and fully trained.
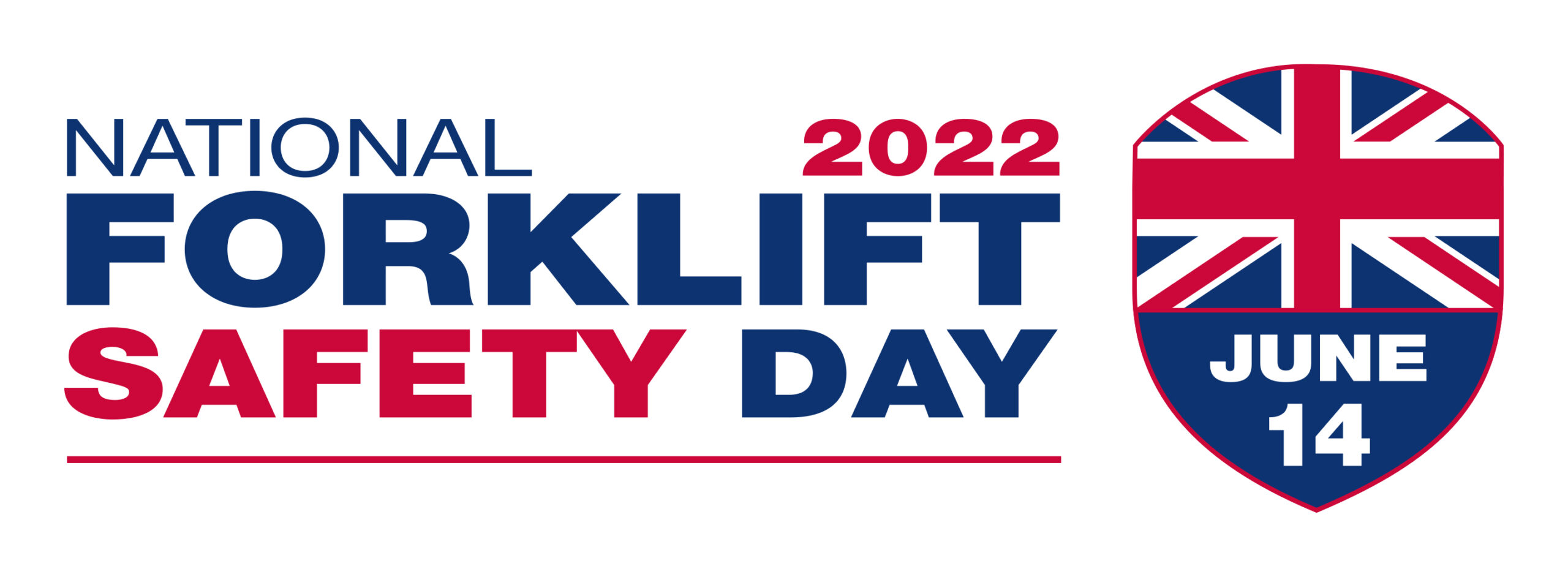
THE LAW
Employers have a general duty under Section 2 of the Health and Safety at Work etc. Act 1974 and under The Management of Health and Safety at Work Regulations 1999 to provide information, instruction, training, and supervision to ensure the health and safety of their employees.
Regulation 9 of The Provision and Use of Work Equipment Regulations 1998 (PUWER), requires employers to ensure that all persons who use work equipment (including forklift trucks) have received adequate training for purposes of health and safety, including training in the methods which may be adopted when using the work equipment, any risks which such use may entail and precautions to be taken.
Sites operating fork lift trucks, or other lifting equipment, are required to comply with The Lifting Operations and Lifting Equipment Regulations 1998 (LOLER) which requires lifting operations to be planned and supervised by suitably competent persons. For many day-to-day operations, the lift may be planned by the operator, so they should have the appropriate training, knowledge and expertise. However, for unusual complex tasks or situations, specific risk assessments and planning are likely to be required.
APPROVED CODE OF PRACTICE
The Health and Safety Executive’s (HSE) Approved Code of Practice and Guidance L117 Rider-operated Lift Trucks is aimed at employers and those responsible for the safe operation of fork lift trucks, as well as those in control of worksites, the self-employed, managers and supervisors.
Although the scope of L117 is limited to rider-operated stacking lift-trucks, the general principles can be applied to other truck types including pedestrian-operated trucks, straddle carriers and ‘stand-on’ pallet trucks) that do not lift materials for stacking will also need training.
Forklift truck operator training is to be consistent with the standards outlined in ACOP L117.
While ACOP L117 is not law, it has been produced under section 16 of the Health and Safety at Work etc Act. 1974 and has special status in law.
FORKLIFT DRIVING LICENSE
AuthorisationIn the UK, there is no such thing as a forklift licence.
Employers and site operators should not allow anyone to operate a forklift on any premises without authorisation.
Authorisation should only be provided after successful completion of all required training elements and should be documented, including:
- Operator’s name
- Date of authorisation
- Types and categories of truck, attachment, load and lifting operation
- Site details
- Any special conditions or restrictions
Agency Workers & Contractors
Employer’s and site operator’s health and safety responsibilities extend to agency workers and contractors.
Whist the content and duration of training may be varied in light of the operator’s experience, evidence of basic training should be provided, and specific job training and familiarisation training will still be required before authorisation is provided.
Public Highway
For operation on the public highway a driving licence is required in addition to the standard training requirements.
When the forklift truck is registered as a “works truck” there is a special case in the legislation which permits a person holding a full category B (car) licence to drive it on the public highway irrespective of the mass limit normally applicable to category B. However, minimum age limits apply as follows: i) Industrial trucks of less than 3.5 tonnes (MAM) – 17 years ii) Industrial trucks over 3.5 tonnes and under 7.5 tonnes (MAM)- 18 years iii) Industrial trucks over 7.5 tonnes (MAM)- 21 years Note: “MAM” relates to the “Maximum Authorised Mass” which is the truck’s total weight plus the maximum load it can carry. For general information about operation of industrial trucks on public roads please refer to BITA GN57.
Overseas Operator Licences
Some countries do issue licences to forklift truck operators. It is quite common for an individual from one of these countries, who is seeking employment in UK as a forklift truck operator, to offer this licence, with an authenticated translation, as proof of their ability to operate.
Operator licences issued outside the UK cannot replace the training and authorisation requirements outlined in this document. Whilst it is possible that they may provide sufficient evidence of basic training, where there is any doubt, employers should arrange an assessment of the person’s competence and provide any necessary training and re-assessment before allowing them to operate a lift truck.
CATEGORIES OF TRUCK
General
The Accrediting Bodies Association for Workplace Transport (ABA) provides standard workplace transport groupings, e.g. B1, Rider operated counterbalance lift truck up to and including 5 tonne.
Training for one group does not provide competence for other groups even if they are similar. However, the duration and content of conversion training may be adjusted to account for previous experience.
Lorry mounted trucks
Site operators should ensure that delivery drivers loading/unloading their own transport by means of lorry-mounted trucks are competent, and have received instruction in the site safe working practices, including identification of hazards, vehicle and pedestrian routes, and site rules, before authorising operations to commence.
Hand pallet trucks Manual and semi-manual pallet trucks are workplace equipment within the scope of PUWER. The employer is obliged to provide adequate training for the purposes of health and safety, including: training in the methods which may be adopted when using work equipment, any risks which such use may entail, and precautions to be taken before, during and after operation.
The degree of training required, and the time it will take, will vary according to the type of equipment and the tasks to be performed.
OPERATOR SELECTION
Medical Standards There is no specific legislation on medical standards for forklift operators, however, they should be reasonably fit, both physically and mentally.
DVLA advice on medical standards for fitness to drive for Group 1 entitlement (ordinary driving licence) can be used for guidance, but fitness to drive for Group 2 entitlement (heavy goods vehicle) should be considered for demanding environments, e.g. shift work, ATEX, complex lifting operations.
Fitness for operating should always be judged on a case-by-case basis: matching the requirements of the task with the fitness and abilities of the operator.
People with disabilities need not be excluded from work as forklift truck operators, and they may have developed compensatory skills. Assessing fitness individually should help ensure that people with disabilities are not disadvantaged.
Reasonable adjustment to work equipment may enable a disabled person to operate workplace transport safely. However, you must always think about their competence in an emergency and, people selected to operate forklift trucks should be free from disabilities, either physical or psychological, that might pose a threat to their own health and safety or the safety of others who might be affected by them operating forklift trucks.
Age Limits
Children under the age of 16 should never be permitted to operate lift trucks. Restrictions and special conditions apply for young persons under the age of 18. Refer to FS01 for further information.
Age limits relating to Maximum Authorised Mass apply when operating works trucks on the public highway.
REQUIRED TRAINING
Basic training
Basic training should cover the skills and knowledge needed to safely operate all of the types of forklift truck and handling attachments the trainee will be required to use.
Realistic loads and a working area representative of actual site conditions should be utilised, and all operational and associated tasks should be covered, e.g. pre-use inspections, refuelling, stacking, refuelling, etc.
This training should be conducted in an area away from other trucks, obstacles, and pedestrians, for example at a suitable training centre or in a segregated area within the employer’s premises.
Upon completion of basic training, the trainee should be assessed to ensure that they have achieved the required standards and are aware of the risks associated with lift truck operations.
Satisfactory completion of basic training does not provide competence to operate forklift trucks unless and until the specific job training and familiarisation training are also successfully completed.
To ensure consistent standards, both in quality and content, UKMHA recommends that basic training should be provided by an accredited training provider.
Specific job training
Specific job training will normally follow the completion of basic training, although it might sometimes be combined or integrated with it. It should be tailored to the specific equipment, loads, operations and site conditions where the trainee will work, and should include:
- Operation and control of the specific forklift truck and attachments to be used.
- Routine inspection and maintenance to be carried out by the operator.
- The actual operating environment, including, for example, gangways, loading bays, racking, automatic doors; cold stores; slopes; other vehicles; and bad weather.
- Site rules, such as one-way systems, speed limits, general emergency procedures, etc.
- Specific hazards, for example pedestrian crossing points, excavations and overhead obstructions or power lines.
- Training in the actual work to be carried out, for example, loading particular types of vehicle, handling loads and materials normally found at that workplace, including assessing weight.
- Safe systems of work, including refuelling, use of operator restraints and leaving vehicles safe and secure.
When the work circumstances change, for instance, by introduction of a new load, process or attachment, additional specific job training must be provided.
Familiarisation training
A period of familiarisation training, carried out on the job and under close supervision, must take place after satisfactory completion of the specific job training.
CONVERSION AND PRIOR TRAINING
Experienced and trained operators can undertake conversion training to extend the categories of truck they are authorised to operate.
Conversion training should include the three training elements of basic, job specific and familiarisation training, but the content and duration of each element should be determined on a case-by-case basis. Testing and authorisation should take place at the conclusion of the training.
When assessing claims of training and experience prior to the commencement of the term of employment, the employer should require evidence that this is sufficient and relevant. Where there is any doubt, employers should arrange an assessment of the person’s competence and provide any necessary training and re-assessment before allowing them to operate a lift truck.
SERVICE ENGINEERS & SALES STAFF
Anyone who operates a forklift truck even on an infrequent basis, needs training to a recognised standard, including engineers, sales personnel and FLT delivery drivers (e.g. HGV drivers). It is crucial that these groups understand how to operate safely, as their job roles often require them to work at customers’ sites. Frequently this training is “restricted”, so as to cover only the operational elements necessary for their intended activities. “Restricted” training is not adequate for full and unlimited operation.
Site operators should ensure that visiting engineers and sales staff are competent, and have received sufficient instruction in the site safe working practices, including identification of relevant hazards, vehicle and pedestrian routes, and site rules, before authorising operations to commence.
MANAGER & SUPERVISOR TRAINING
Although employers and supervisory staff are not required to be qualified forklift truck operators, they must have sufficient knowledge of the operational characteristics and hazards of forklift operations to maintain a safe working environment and to intervene in order to stop any bad practices or behaviours from taking place.
Even experienced, fully trained forklift truck operators require supervision and monitoring to ensure they are working correctly and safely and determine whether retesting or refresher training is necessary.
Supervisor training can reduce the risk of incident and injury and delivers financial benefits, by reducing damage to stock, equipment, fixtures, fittings whilst improving the productivity and efficiency of fork lift truck operations.
MONITORING & ASSESSMENT
Employers should have routine monitoring and assessment processes to ensure that refresher training and retesting is promptly implemented as required.
Monitoring should check for any developing unsafe working practices, changes in working practices or environment, and accidents and near-misses.
Assessments should be carried out by a suitably competent person to determine whether refresher training is required.
REFRESHER TRAINING
Refresher training is legally required and can be the best way to make sure employees stay competent.
There is no defined time period after which an employer must provide refresher training; it should be in line with company polices following the completion of a risk assessment, but the accredited training establishment providing the initial training should be able to assist with this.
A common interval for refresher training is 3-5 years, however, this will depend on the specific circumstances and will need to be reduced if performance monitoring indicates a requirement.
Refresher training might also be appropriate where the operator has not used trucks for some time.
TRAINING RECORDS
Employers and site operators should maintain records of authorisations, training and assessments, including conversion and refresher training.
Records should identify names, dates, equipment and training providers, along with any limitations or expiry dates.
Employers are not under a statutory duty to furnish training records to their employees or to third parties, however, in accordance with HSE guidance, it is best practice to at least provide the employee with an ‘original’ certificate of basic training with some means of establishing its validity.
ACCREDITED TRAINING PROVIDERS
There are a number of organisations who provide accreditation for lift-truck training schemes, and they are represented by Accrediting Bodies Association for Workplace Transport (ABA), see Appendix II for details. These schemes are intended to:
- Help set and maintain professional training standards.
- Help employers select training organisations or lift-truck suppliers who offer a good standard of training.
Accrediting bodies deem competent organisations or individuals as ‘accredited training providers’ (ATP).
An ATP may be an organisation, individual, or an in-house training scheme. The main conditions of accreditation are that ATPs use qualified and experienced instructors only, that they follow course syllabuses approved by the accrediting body and that they be subjected to regular monitoring visits by the accrediting body.
Certificates issued by an ATP will quote their accreditation number, the name of the accrediting body, and the name and registration number of the instructor who conducted the training.
Certificates should always provide sufficient information to allow the training to be traced back to course content. If training has been limited (e.g. lifting to 3 metres), then the certificate should identify this limitation to ensure operators only undertake work for which they have been trained.
Note that there is no legal requirement for certificates, which are often confused with licences, but ATPs will always issue them and HSE encourages their use as a good way of demonstrating that training has been provided. Remember there is no such thing as a forklift truck licence.
ACCREDITED TRAINING PROVIDERS
There are a number of organisations who provide accreditation for lift-truck training schemes, and they are represented by Accrediting Bodies Association for Workplace Transport (ABA), see Appendix II for details. These schemes are intended to:
- Help set and maintain professional training standards.
- Help employers select training organisations or lift-truck suppliers who offer a good standard of training.
Accrediting bodies deem competent organisations or individuals as ‘accredited training providers’ (ATP).
An ATP may be an organisation, individual, or an in-house training scheme. The main conditions of accreditation are that ATPs use qualified and experienced instructors only, that they follow course syllabuses approved by the accrediting body and that they be subjected to regular monitoring visits by the accrediting body.
Certificates issued by an ATP will quote their accreditation number, the name of the accrediting body, and the name and registration number of the instructor who conducted the training.
Certificates should always provide sufficient information to allow the training to be traced back to course content. If training has been limited (e.g. lifting to 3 metres), then the certificate should identify this limitation to ensure operators only undertake work for which they have been trained.
Note that there is no legal requirement for certificates, which are often confused with licences, but ATPs will always issue them and HSE encourages their use as a good way of demonstrating that training has been provided. Remember there is no such thing as a forklift truck licence.
APPENDIX: ADDITIONAL RESOURCES
HSE INDG457 Use lift trucks safely. Advice for operators
HSE INDG462 Lift-truck training. Advice for employers
HSE HSG136 A guide to workplace transport safety
DVLA Assessing fitness to drive – a guide for medical professionals
FS1 What is the Minimum Age for Operating Forklift Trucks
FS2 How Long Does a Fork Truck Driver’s Licence Last
FS6 Forklift Operator Training – Recognised Accrediting Bodies
FS9 Training Requirements for Hand Pallet Trucks
FS12 The Legal Requirements for Forklift Truck Operator Refresher Training
FS16 Overseas Forklift Truck Operator Licences
FS19 Medical Standards for Forklift Truck Operators
FS23 Forklift Truck Operator Training
FS24 Supervision of Forklift Truck Operations
FS28 Forklift Truck Operator Daily Checks
FS30 Operator Training for Forklift Truck Engineers and Sales Personnel etc.
B.01 BITA Operator’s Safety Code for Powered Industrial Trucks
B.04 Do’s & Don’ts for Users of Industrial and Rough Terrain Lift Trucks
BITA GN57 Industrial trucks on public roads
ABA Workplace transport groupings
ABA Basic Operating Skills Test. Rider Operated Counterbalance and Reach Lift Trucks
ABA Basic Operating Skills Test. Pallet/Stacker Truck
ABA Basic Operating Skills Test. Medium and High Level Order Picker
ABA Basic Operating Skills Test. Rider Operated Very Narrow Aisle Lift Truck
BS ISO 21262:2020 Industrial trucks — Safety rules for application, operation and maintenance